Injection systems serve an import roll. Injection systems are used to meter and distribute many different types of dry sorbents and products into boilers, furnaces, fabric filters, precipitators, flue gas ducts and other reaction zones.
Typical Products Injected:
-
Limestone
-
Hydrated Lime
-
Trona
-
Sodium Bicarbonate
-
Activated Carbon
-
Fly Ash
-
Dry Sorbents
-
Inert Products
-
Alkaline Reagents & More...

.png)
InjectionFeed
Clyde Pneumatic Conveying
The Clyde Pneumatic Conveying Injectionfeed Injection technology is engineered to deliver highly precise and consistently controlled batch or continuous material injection directly into process environments, such as blast furnaces, power boilers, or similar applications.

Material is fed from a dispensing vessel via the Injectionfeed, powered by a variable-speed electric motor to regulate material flow into the injection pipeline.
Key Features:
-
Continuous or Batch Feed: Allows for both continuous or batch injection when equipped with a lock hopper.
-
Wide Control Over Feed Rate: Variable-speed motor enables a 10:1 system turndown or ramp-up for flexible control.
-
High Accuracy in Injection Rates: Achieves 1-2% accuracy by weight (gravimetric) with load cells, and 5-10% (volumetric) without load cells.
Benefits:
-
Exceptional Reliability: Built with proven components, ensuring dependable performance across diverse applications.
-
High Availability: Capable of over 3,000,000 cycles before major overhauls and 1,000,000 cycles for seal replacement.

ROTOSCREW Screw Injector
Clyde Pneumatic Conveying
Key Features:
-
Pelletised, Granular materials > 10mm
-
Suitable for abrasive materials
-
For injection rates from 0.5m³/h up to 90m³/h
-
Uses standard AC induction motor controlled by
-
Variable Frequency Drive to give fully variable
-
output within the turndown range.
-
5:1 turndown ratio as standard, 10:1 if required
-
Volumetric accuracy +/-2%
-
+/-0.5% by weight by using a loss in weight system
-
Operates at zero pressure differential eliminating wear
-
Capable of high pressure applications 40barg or more


Innovations for Reducing Acid Gas and Emissions Control
Since the 1980s, Delta Ducon has led the way in acid gas reduction through pioneering injection system technology. With hundreds of installations across industries like cement, mineral processing, and power, Delta Ducon’s systems effectively control pollutants like SO₂, SO₃, HCl, and mercury, providing a sustainable solution for environmental compliance. Utilizing materials such as activated carbon, hydrated lime, and sodium bicarbonate, these systems are easy to automate and install, offering a cost-effective option for businesses. As decarbonization becomes more essential, Delta Ducon remains a trusted partner for reducing emissions and supporting greener industrial operations.
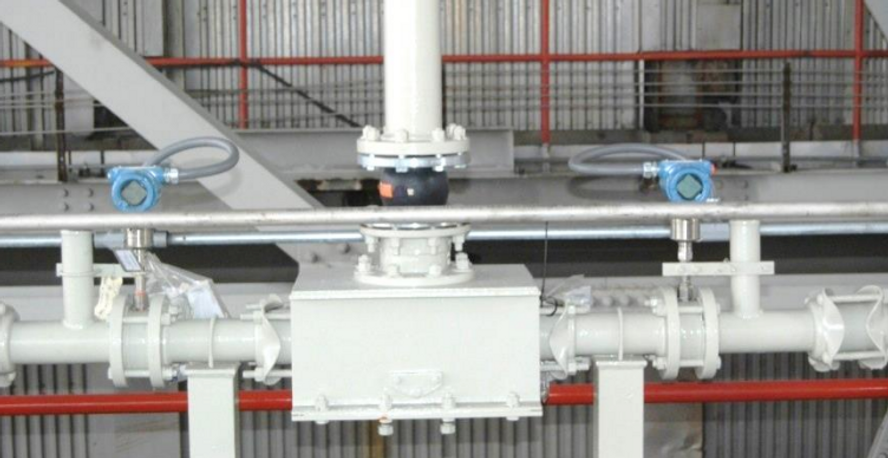
Injection systems are used to control pollutants such as SO2 , SO3 ,HCl & Mercury. They are typically required to operate continuously, 24 hours per day, and are required to be reliable with zero to minimal down time. For this reason Delta Ducon equipment has been used in hundreds of injection systems. Our patented flow splitters and superior rotary valves are key components for injection systems.

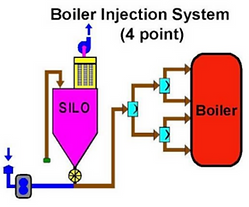

Products in the system
