Troubleshooting Pneumatic Conveying Systems: Common Problems and Solutions
- Delta Ducon
- Jan 5
- 3 min read
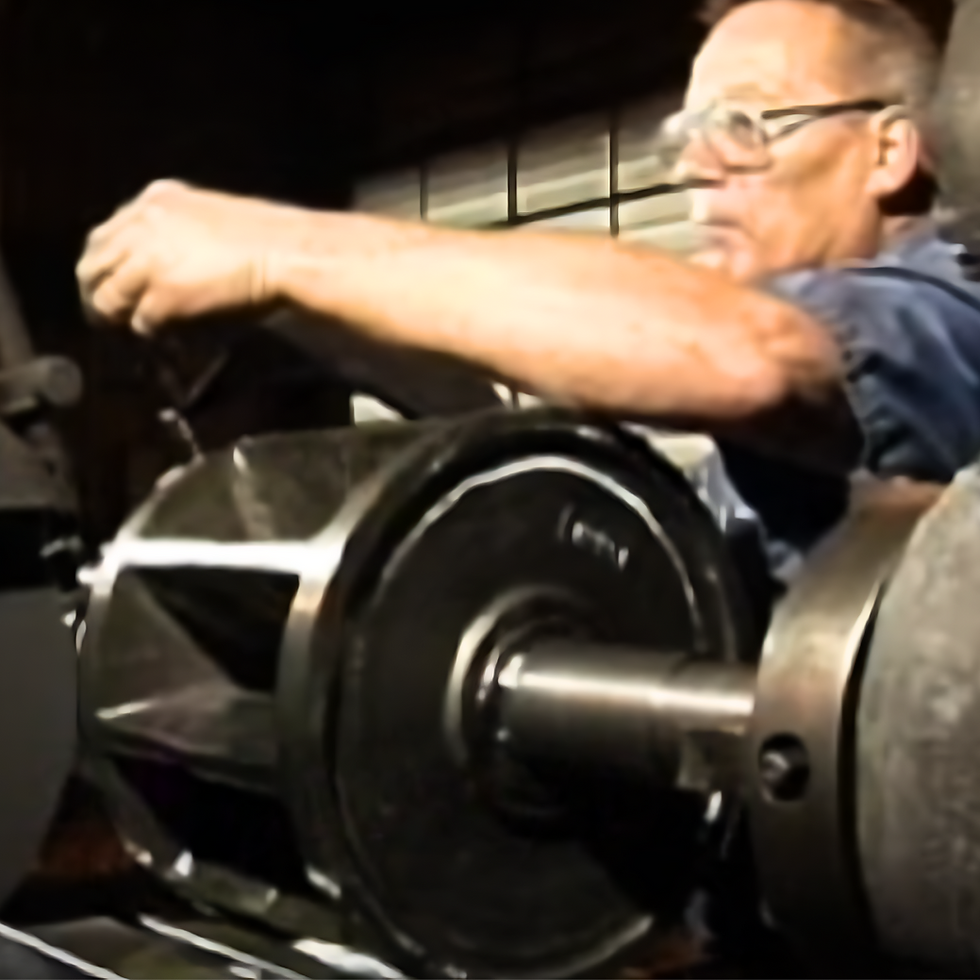
Pneumatic conveying systems are vital for efficient material handling across various industries. However, like any complex system, they can encounter operational issues that require troubleshooting and maintenance. Let's explore some of the most common problems in pneumatic conveying systems and how Delta Ducon can help you address them.
1. Plugging and Blockages:
Material buildup and blockages are common culprits in pneumatic conveying systems, disrupting material flow and hindering productivity. They can occur due to various factors, including:
Moisture: Material with high moisture content can clump together, causing blockages.
Particle size and shape: Irregularly shaped or excessively fine particles can create bridges or adhere to pipe walls, leading to buildup.
Low air velocity: Insufficient airspeed may cause material to settle and accumulate in the pipeline.
Delta Ducon Solutions:
System Design: We optimize system design to ensure adequate air velocity and minimize areas prone to material buildup.
Material Selection: We assist in selecting appropriate materials for pipeline construction, considering factors like abrasion resistance and smooth internal surfaces.
Specialized Components: We offer components like airlocks and specialized rotary valves to prevent material backflow and ensure consistent flow.
2. Wear and Tear:
The abrasive nature of conveyed materials, coupled with high conveying velocities, can cause wear and tear on system components, particularly pipelines, bends, and rotary valves.
Delta Ducon Solutions:
Durable Materials: We utilize wear-resistant materials like hardened steel alloys for critical components, extending their service life.
Innovative Designs: Our Extreme Rotary Valves feature durable components like P-33 alloy rotors and heavy-duty housings to withstand abrasive wear.
Preventative Maintenance: We provide guidance on preventative maintenance practices to minimize wear and tear and extend equipment lifespan.
3. Air Leaks:
Leaks in pipelines, connections, or seals can significantly reduce conveying efficiency, leading to pressure loss, increased energy consumption, and potential material spills.
Delta Ducon Solutions:
System Inspections: We conduct thorough system inspections to identify and address potential leak points.
Proper Sealing: We ensure proper sealing of connections and utilize high-quality gaskets and seals to prevent leaks.
Leak Detection: We offer leak detection services to identify and address leaks promptly, minimizing downtime and material waste.
4. Inadequate Air Supply:
Insufficient air supply from the blower or compressor can hinder system performance, leading to reduced conveying capacity and potential material buildup.
Delta Ducon Solutions:
Proper Blower Selection: We assist in selecting the right blower or compressor for your specific application, ensuring adequate air supply and pressure.
System Monitoring: We offer monitoring systems to track air pressure and flow, allowing for prompt detection and resolution of air supply issues.
5. Material Degradation:
Fragile materials can be susceptible to degradation during pneumatic conveying due to particle attrition or excessive pressure.
Delta Ducon Solutions:
Gentle Conveying: We design systems with appropriate air velocities and pressure settings to minimize material degradation.
Dense Phase Option: We offer dense phase conveying solutions for fragile materials, where materials move in a slower, more controlled manner, reducing the risk of damage.
Delta Ducon: Your Partner in Maintenance and Troubleshooting
With our extensive experience in pneumatic conveying, Delta Ducon offers comprehensive solutions to address common system problems. Our expert engineers, high-quality components, and commitment to customer support ensure efficient and reliable operation of your pneumatic conveying system.
Contact us today to discuss your maintenance and troubleshooting needs. We'll help you identify potential issues, implement preventative measures, and ensure optimal performance of your pneumatic conveying system.
Comments