Optimizing Clinker Transport: A Comprehensive Pneumatic Conveying Approach
- Delta Ducon
- Feb 11
- 3 min read
Introduction
Clinker, a crucial intermediate material in cement production, presents unique challenges for material handling due to its abrasive nature and high temperatures. Traditional mechanical conveying methods often lead to excessive wear and tear on equipment, resulting in increased maintenance costs, downtime, and potential product degradation. Pneumatic conveying has emerged as a viable alternative, offering a gentler and more efficient means of clinker transport. This white paper explores the challenges of conveying abrasive clinker and discusses how optimizing both dense phase and dilute phase pneumatic conveying systems can address these challenges, leading to improved efficiency, reduced wear, and enhanced dust control.
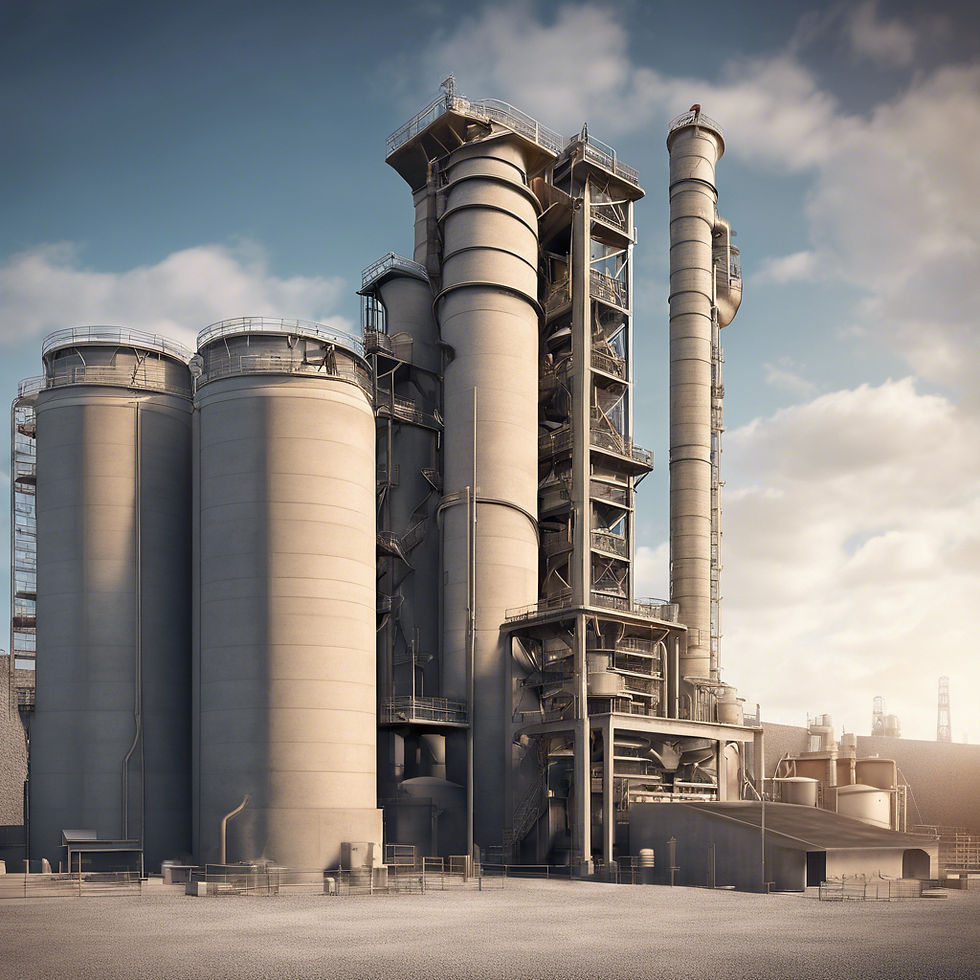
Challenges of Conveying Abrasive Clinker
Clinker, with its sharp edges and irregular shapes, poses several challenges for material handling systems:
Abrasive Wear: Clinker's abrasive nature causes significant wear and tear on conveying equipment, particularly pipelines, bends, and valves. This wear can lead to reduced equipment lifespan, increased maintenance costs, and potential product contamination.
High Temperatures: Clinker exits the kiln at high temperatures, requiring conveying systems that can withstand these extreme conditions. High temperatures can accelerate wear and tear on equipment and pose safety hazards if not properly managed.
Dust Generation: Clinker transport can generate significant dust, posing risks to worker health and the environment. Effective dust control measures are essential to ensure a safe and compliant operation.
Dense Phase Pneumatic Conveying for Clinker Transport
Dense phase pneumatic conveying offers a solution to the challenges of clinker transport. By conveying material at lower velocities and higher solids-to-air ratios, dense phase systems minimize the abrasive forces and reduce wear and tear on equipment.
Key considerations for optimizing dense phase conveying for clinker transport include:
System Design: Proper system design is crucial for efficient and reliable clinker transport. This includes selecting appropriate pipe diameters, minimizing bends and changes in direction, and ensuring proper material flow to prevent buildup and blockages.
Component Selection: Choosing wear-resistant components, such as hardened rotary valves, abrasion-resistant piping, and durable blowers, is essential for extending the life of the system and minimizing maintenance needs.
Dust Control: Implementing effective dust collection systems at various points in the conveying process is crucial for minimizing dust emissions and ensuring a safe and compliant operation.
Temperature Management: Incorporating measures to manage clinker temperature during transport, such as insulation or cooling systems, can help reduce wear and tear on equipment and prevent safety hazards.
Dilute Phase Pneumatic Conveying for Clinker Transport
Both dense phase conveying and dilute phase conveying can be viable options for clinker transport depending on the criteria your system.
Key considerations for optimizing dilute phase conveying for clinker transport include:
System Design: Proper system design is crucial for minimizing wear and tear in dilute phase systems. This includes selecting appropriate air velocities, minimizing bends and changes in direction, and ensuring proper material flow to prevent buildup and blockages.
Component Selection: Choosing wear-resistant components, such as hardened elbows, bends, and diverters, is essential for extending the life of the system and minimizing maintenance needs.
Specialized Pipe: Utilizing specialized pipe options with enhanced wear resistance, such as ceramic-lined pipe or pipe with hardened internal surfaces, can significantly extend the lifespan of the system and reduce maintenance needs.
Advanced Monitoring and Control: Implementing advanced monitoring and control systems can help optimize system performance and minimize wear and tear by adjusting air velocity and pressure based on real-time conditions.
Delta Ducon's Expertise
Delta Ducon, a leading provider of pneumatic conveying solutions, has extensive experience in designing and implementing both dense phase and dilute phase conveying systems optimized for abrasive materials like clinker. Our expertise includes:
Dense Phase Solutions: We offer a complete line of heavy-duty rotary valves, abrasion-resistant piping, and advanced control systems designed for dense phase conveying of abrasive materials.
Dilute Phase Solutions: We provide wear-resistant components, specialized pipe options, and advanced monitoring and control systems to optimize dilute phase conveying for abrasive applications.
System Design and Engineering Expertise: Our experienced engineers can design and optimize both dense phase and dilute phase conveying systems tailored to your specific needs, ensuring efficient and reliable operation.
Conclusion
Both dense phase and dilute phase pneumatic conveying offer viable solutions for transporting abrasive clinker in cement production. Dense phase conveying excels in minimizing wear and tear, while dilute phase conveying can be advantageous for shorter distances and with careful optimization. By partnering with a trusted provider like Delta Ducon, you can leverage our expertise and innovative solutions to optimize your clinker transport system for maximum efficiency, reliability, and longevity.
Comments